FLUID HEAT TRANSFER SYSTEMS
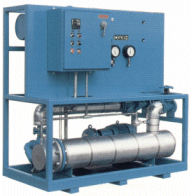 |
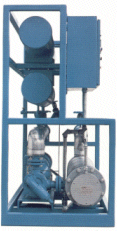 |
Fluid heat transfer systems are complete and ready to be installed providing exact and uniform temperatures. These systems contain heater, solid state controls, pump, valves and necessary piping to pump heat transfer fluid. Suitable for closed loop heating of platens, dies and molds, jacketed vessels and tanks, revolving rolls or for heating of viscous chemicals or petrochemicals to maintain pumping temperatures or for freeze protection. Correct ratio of flow rate versus kilowatt rating assures continuous and consistent process temperatures. |
- Can be used with most heat transfer fluids to 450°F/230°C maximum operating temperature.
- Low watt density heating elements welded into a 150 Ib. ASA steel flange and mounted in an all welded steel chamber.
- Horizontal mounting of heating chamber eliminates air contamination and manual venting.
- Buffer tank is provided between heating chamber and expansion tank to help prevent degradation of heat transfer fluid.
- Expansion tank above buffer tank for cold oil, vented to atmosphere with sight glass.
- Inlet and outlet connection equipped with manually operated valves should system need to be isolated from process.
- 2" insulation with metal jacket on all piping.
- Flexible stainless steel hoses on suction and discharge of pump to absorb vibration.
- Rotary gear pump with by-pass for temperatures to 450°F/230°C. Mechanical seal eliminates constant dripping associated with standard "wet seal" pumps.
|
- In-line rotary gear reducer reduces noise in system and maintains pump below 500 RPM's for long life.
- Vacuum and suction gauges installed in system.
- Thermocouple well assembly installed in outlet for process control.
- Thermocouple installed on heater sheath for overheat protection.
- NEMA Xll Control Panel.
- Door mounted disconnect handle, motor and heater pilot lights and switches.
- Indicating electronic temperature control.
- Pump circuit separately fused with full voltage non-reversing motor starter.
- Electronic high-limit control with separate safety contactors and illuminated reset button.
|
|